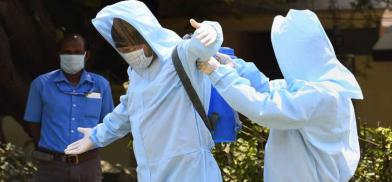
Plastic from used personal protective equipment (PPE) can and should be transformed into renewable liquid fuels, according to Indian researchers. The study, published in the journal Biofuels, suggested a strategy that could help to mitigate the problem of dumped PPE - currently being disposed of at unprecedented levels due to the current COVID-19 pandemic - becoming a significant threat to the environment.
The research from the University of Petroleum and Energy Studies (UPES) in Uttarakhand shows how billions of items of disposable PPE can be converted from its polypropylene (plastic) state into biofuels - which is known to be at par with standard fossil fuels. "The transformation into biocrude, a type of synthetic fuel, will not just prevent the severe aftereffects to humankind and the environment but also produce a source of energy," said study lead author Dr Sapna Jain from UPES.
There is high production and utilisation of PPE to protect the community of health workers and other frontline workers of COVID-19. The disposal of PPE is a concern owing to its material i.e. non-woven polypropylene. "The proposed strategy is a suggestive measure addressing the anticipated problem of disposal of PPE," Jain said.
During the current COVID-19 pandemic specifically, PPE is being designed for single-use followed by disposal. Once these plastic materials are discharged into the environment they end up in landfills or oceans, as their natural degradation is difficult at ambient temperature. They need decades to decompose.
Recycling these polymers requires both physical methods and chemical methods. Reduction, reuse and recycling are the three pillars of sustainable development that can help to prevent the disposal of plastic in the environment. The research team reviewed many related research articles as they looked to explore the current policies around PPE disposal, the polypropylene content in PPE, and the feasibility of converting PPE into biofuel.
In particular, they focused on the structure of polypropylene, its suitability for PPE, why it poses an environmental threat and methods of recycling this polymer. Their conclusive findings call for the PPE waste to be converted into fuel using pyrolysis. This a chemical process for breaking down the plastic at high temperature - between 300-400 degrees centigrade for an hour - without oxygen.
According to the researchers, this process is among the most promising and sustainable methods of recycling compared with incineration and landfill.
"Pyrolysis is the most commonly used chemical method whose benefits include the ability to produce high quantities of bio-oil which is easily biodegradable," said study co-author Bhawna Yadav Lamba.
"There is always a need for alternative fuels or energy resources to meet our energy demands. The pyrolysis of plastics is one of the methods to mitigate our energy crisis," she noted.(IANS)